Order processing is one of the stages of eCommerce logistics that has the biggest impact on costs. Do you want to know what ‘order processing’ means? In this article, you’ll learn the definition and the 5 steps that make up order processing, as well as how you can optimize and automate order processing with software and other tools.
What does order processing mean?
Order processing involves all the tasks that need to be carried out to ship products from the warehouse to the customer.
Some of these tasks are picking and packing, along with the processes that fit within them, such as labelling, quality control and even shipping.
If you sell products online, you probably already know that order processing is an essential activity for the success of your business. Not only does it guarantee that the customer receives the products within the agreed period and without damages, but it also reduces logistics costs, increasing your profit margins.
Cutting resources in order processing can be extremely expensive in the long run since it will cost you brand image and reputation, and affect fulfilment, customer service and marketing costs.
What happens when you receive an order?
When a customer makes a purchase, the seller will receive an order notification to start the processing stage. The different activities within order processing will be further explained below.
Once the order has been handed over for delivery, the customer will automatically receive a notification if the seller has the tools for it.
Order processing in 5 steps
1. Planning
During this stage, the strategy is designed and the order data is filtered for more efficient performance in the order processing process.
2. Picking
The picking stage refers to the action of taking all the items that make up the order from the inventory. Depending on the dimensions of the products or the warehouse, the picker may need special machinery or software for traceability of the routes and products.
3. Verification
The verification stage consists of confirming that the picked items are the products requested by the customer. Once the items have been verified, the next step is to generate the shipping label that will be attached to the package.
4. Packing
In the packing stage, items are packed and the parcel is sealed, weighed and labelled. For international shipping, additional documentation will be needed, such as a commercial invoice.
5. Shipping
The parcel is handed to the shipping company. This courier will be in charge of delivering it to the final customer.
7 Tools for order processing
1. Order processing software
Order processing software gathers and stores information related to orders, customers and the business itself. This information can be used to optimize order processing tasks such as picking and packing, labelling or shipping. Ideally, these software systems help automate manual operations, minimizing human errors and ultimately improving customer experience and business performance and profitability.
2. Machinery
Pallet trucks and order pickers allow the operator to move multiple heavy items in a faster and safer way. Any large warehouse will need, at the very least, rudimentary machinery for the picking process.
3. Automated guided vehicles (AGV)
Automated guided vehicles, or AGVs, can be used to speed up the picking and packing in more complex supply chains thanks to a more autonomous collection system in the warehouse.
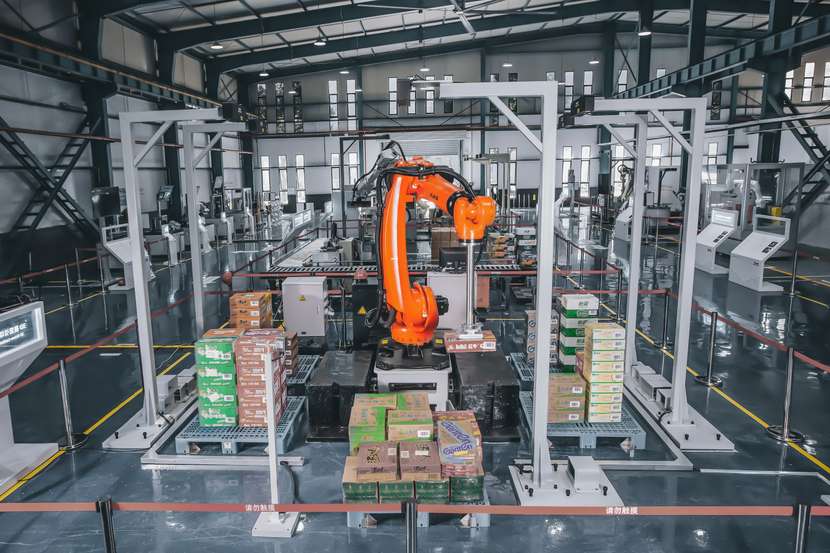
4. Automatic rails
Automatic rails connect different parts of a warehouse, allowing for a better flow of goods along the rails.
5. Automated shelves
These shelves or racks include technology to select and move the products from their location in the warehouse to the hands of the operator for the packing stage.
6. Enterprise resource planning (ERP) system
An ERP system can be used to optimize business processes by providing a point for information collection available for all departments. ERP systems help monitor and prioritize customers and customer data, improving order processing speed and, therefore, the customer experience.
7. Warehouse management system (WMS)
A warehouse management system, or WMS, helps businesses manage several warehouse-related tasks. Typically, they are used in conjunction with an ERP and other types of software systems to further streamline the order processing flow, increasing the quality of the service while also reducing costs.
The best order processing software for automation
Outvio has designed all the required tools for efficient order processing, from picking lists to order classification, courier comparison and automatic label printing. This speeds up processing times and eliminates unnecessary costs.
Common errors in the processing of orders
- Wrong product (or wrong color or size)
- Wrong number of items per order
- Wrong packaging for the product, causing damages and claims
- Lengthy order processing
Documents required for order processing
- Picking list: This document includes all the items that need to be collected in the warehouse. It also includes the quantity, the order number and even the exact location of the item in the warehouse.
- Packing list: similar to the picking list, but designed for the packing stage.
- Delivery note: This document works as proof of the delivery to the courier. It’s essential to be able to make a claim for loss or damage.
- Waybill: This shows the transport and delivery routes that the courier will follow. This can speed up last-mile deliveries and help avoid shipping issues.
- Tracking number: A numerical sequence linked to every order to allow package tracking. This number is normally provided by the shipping company.
- Customs documents: If you make international shipments, you’ll need to include additional documents. They will vary depending on legislation and the courier you work with. To learn everything you need about customs documents, read our article on customs clearance.
Order processing FAQs
What is the order processing area?
Ideally, every business that physically manages items should have an area designated for the handling, picking and packing of products in a safe and efficient way. In your order processing area, you can establish a specific spot for packing, another for quality control and another for labelling. Of course, this may vary depending on the size of your company.
How do you improve order processing?
You can improve order processing with tools, both physical and virtual, to automate, speed up and optimize repetitive tasks that are a common source of human errors. For instance, using order processing software and special machinery are some common practices to improve order processing.
How can you avoid errors while processing orders?
Automating processes is the safest way to avoid errors in the processing stage since most of the errors tend to be caused by human carelessness.
How can order processing software help my business?
Order processing software helps businesses in two ways:
- Order processing software provides more traceability for incoming and outgoing orders, data collection and communication tasks. This means fewer errors and, therefore, fewer costs.
- Order processing software can also be used as an opportunity to improve communication between your business and your customers. Customers’ information and advanced tools will help you personalize the message and improve customer experience since orders will be processed faster and with fewer inaccuracies, and communications will be fully branded and personalized.
Types of order processing systems
Businesses can choose between two types of order processing systems. They can opt for either a manual order processing system —this is a more traditional approach— or a modern order processing system that is tech-based and automated.