Picking lists are one of the most important and necessary tools for eCommerce order preparation. This document, which can be both physical or digital, optimizes the picking of products in the warehouse, allowing operators to perform the work in an orderly and efficient way.
In this article, we explain how to use a picking list to improve your business results, what are the different formats of picking lists, and how to create them efficiently.
You will also discover that with Outvio’s e-commerce fulfillment software, you can create picking lists automatically and customize them to meet the logistical needs of each order, minimizing your logistics costs.
What is a picking list? Definition
A picking list is an instrument used in logistics to coordinate and optimize the picking of products in a warehouse. It provides detailed instructions on what items to pick, in what order, their location, and the exact quantities.
It is important to note that the information contained and its structure must be adapted tothe type of picking and packing that is to be carried out internally, considering variables such as the selection of individual items, batch grouping, segmentation by zones, and demand level, among other relevant factors.
Benefits of a picking list
As an eCommerce owner, you know that customer satisfaction is essential to the success of your business. A well-designed picking list can help you improve the customer experience and your warehouse operations in several ways:
- Efficiency in picking: A well-optimized picking list can help you reduce the time your employees spend looking for products. This is because the list is generated based on the physical location of the products, which allows your employees to plan their route efficiently.
- Error reduction: A precise picking list can help reduce picking errors. This is because the list includes all the information your employees need to select the right products.
- Improved traceability: A picking list provides detailed traceability of the products selected. This can help you identify problems, such as damaged or missing products.
- Customer satisfaction: Quick and accurate delivery is essential for a good customer experience. A well-designed picking list can help you meet your customers' expectations and improve their satisfaction.
- Improved productivity: A picking list can help improve the productivity of your employees. This is because the list provides them with all the information they need to do their job quickly and efficiently.
- Additional benefits in the warehouse: In addition to the benefits mentioned above, a picking list can also help you improve warehouse safety, reduce waste, and improve inventory management.
What information should be included in a picking list?
A picking list should contain the following information:
- Picking list number:This is a unique identifier for each picking list. It is used to classify the document and prevent duplication.
- Order number: It is important that the picking list includes the order number and its identification. In case of picking products from multiple orders, the number of all of them must be included.
- SKU: The SKU code is the alphanumeric reference number that identifies and manages each product within the inventory.
- Product information: This information helps operators to identify products and avoid confusion. The list usually includes the product name, size, weight, description, and a photograph.
- Location: The picking list must include the warehouse area in which the product is located and the shelf number. This allows operators to organize faster routes.
Examples of picking lists
Let's take a look at some picking list formats or templates:
Paper picking lists
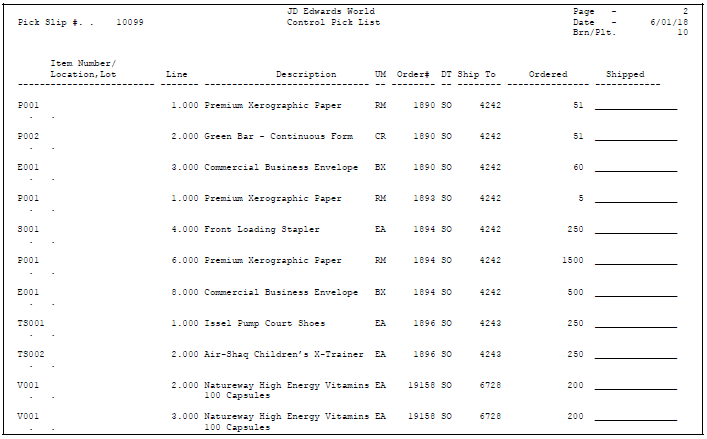
Paper picking lists are a traditional way to organize and manage the order picking process. In this method, operators receive a printed list that contains the details of the products they need to pick and pack.
Features:
- Printed format: Lists are presented on paper, and operators manually consult the necessary information
- Less flexibility: Unlike digital versions, paper lists may be less adaptable to last-minute changes or real-time updates
- Requires more attention:
- Operators must be careful to avoid errors in product identification and quantity to pick
Voice picking lists
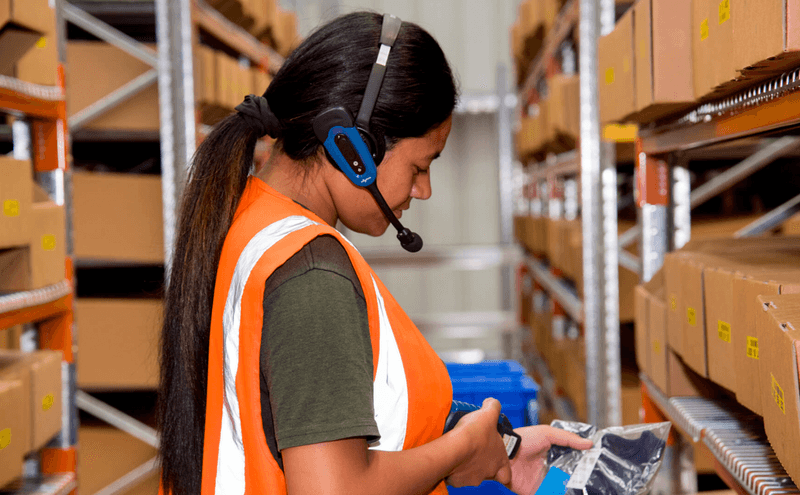
Voice picking lists are a method of inventory management and order picking in a logistics warehouse. Operators use voice communication devices, such as headsets and microphones, to receive instructions during the process.
Features:
- Voice interaction: Operators receive instructions and verbally confirm their execution, which allows them to keep their hands free to pick and pack products.
- Increased accuracy and efficiency: By eliminating the need to refer to printed or digital lists, errors are minimized and productivity is improved.
- Ideal for noisy environments: Works well in places with a lot of ambient noise, as operators can receive instructions and confirm without looking at screens.
Digital Picking Lists
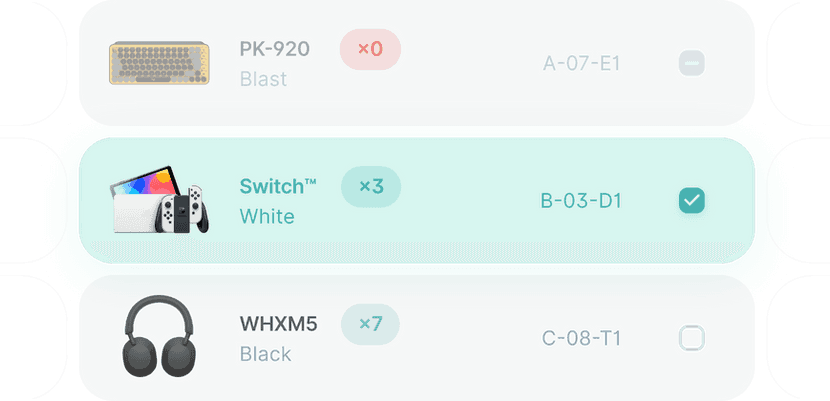
Digital picking lists are electronic and advanced versions of paper picking lists. They are presented on mobile devices, such as tablets or scanners, and allow efficient order management in real time.
Features:
- Flexibility and real-time updates: Digital picking lists can be updated in real time, making it easy to incorporate last-minute changes or new orders.
- Reduced error rate: Automation and the digital interface reduce human errors by minimizing the need for manual input.
- Integration with other systems: Digital picking lists can be linked to wider transportation and logistics management systems, allowing for optimized workflows.
How to Create Picking Lists
Manually Creating Picking Lists
Manually creating picking lists is the simplest and most traditional method. It involves an employee in the warehouse, with access to order information, manually gathering the necessary data to create the list and adding it to an Excel spreadsheet. As we said, this is a very slow process and there is also some risk of human error.
Some important tips:
- Identify each product and its location correctly before creating the list
- Include instructions for your employees in case they need to pick up high-fragility products
- Organize the picking list in a logical order, so that the selected products are located sequentially
- If you use containers to pick up products, number them so that employees can easily identify where to place each item
- Double-check the information it contains
Automatically Creating Picking Lists
The digital or automatic creation of picking lists is the most efficient and accurate method. You simply have to import the order information and the list will be generated automatically.
One of the best pick pack system for creating picking lists and automating fulfillment processes is Outvio. The tool provides everything a company needs to reduce its operational costs and improve work times.
Advantages of Outvio picking lists:
- They are created automatically based on order information. Additionally, they can be customized to fit the specific needs of each warehouse
- They are designed to be clear and legible, making it easier for employees to pick up the products correctly
- They can include additional information, such as the weight or size of the products. This information can be useful for employees when handling products
- Outvio offers performance reports that allow administrators to monitor the performance of the picking process
How to Choose the Best Picking List for Your Warehouse
There are many different types of picking lists available. The type of list you choose will depend on the specific needs of your business.
If you have a small warehouse with a limited selection of products, a manual or paper picking list may be sufficient. However, if you have a large/medium warehouse or a wide selection of products, a digital picking list is your best option.
In summary:
- Automated or digital picking lists use software to generate an optimized picking sequence. This can help you improve picking efficiency and accuracy.
- Manual picking lists, although they do not require investment, can be more difficult to use and can lead to errors and delays.
Conclusion
With a picking list, your employees will know exactly what product to pick and where to find it. You will reduce errors and, as a result, returns will be a thing of the past. Your customers will trust your efficiency and quality of service, and this will translate into recommendations, sales, and greater customer loyalty!